Decoupling operations: what are the benefits?
In a recent article, I discussed the relationship between decoupling and travel distance. In this 2 minute read, I would like to explore the benefits of decoupling, as they are not always seen. Decoupling is the concept of having a buffer (typically a place where a container can stay for a short while until it is picked up by the next mode in the chain) inbetween two consecutive processes. Buffers are an essential logistical concept to reduce the impact of variance (fluctuation of process times: the worst enemy of efficiency). In any logistic process, buffers are required, as variance is unavoidable. It is for a reason that 6 sigma aims at reducing variance in processes!
In a decoupled process, there is a buffer inbetween two consecutive processes. This buffer allows one machine to operate without direct coordination with another machine. Think of an automated stacking crane (ARMG) placing a container in the interchange zone, and 15 minutes later, the shuttle carrier picking up the container, instead of a coordinated handover between an ARMG and a terminal tractor (TT) or AGV. Apart from the waiting time for both machines this coordination causes (the TT / AGV needs to be there before the ARMG can drop the container, or the ARMG waits until the TT / AGV arrives), the “intelligence” of the TOS (Terminal Operating System) needs to be much more sophisticated to ensure a short waiting time for either equipment. Deviations from the expected arrival time of one equipment (e.g. due to traffic congestion) will impact the other equipment immediately. As a consequence, TT / AGV lose about 50% of their transportation capacity due to waiting (they act as the buffer). Which means that the fleet size of transport vehicles in a coupled operation is typically larger than in the decoupled alternative. Also the ARMG loses a part of its capacity due to waiting (as this is the more expensive resource, it is better to let the TT / AGV wait, but still), typically in the range of 10%.
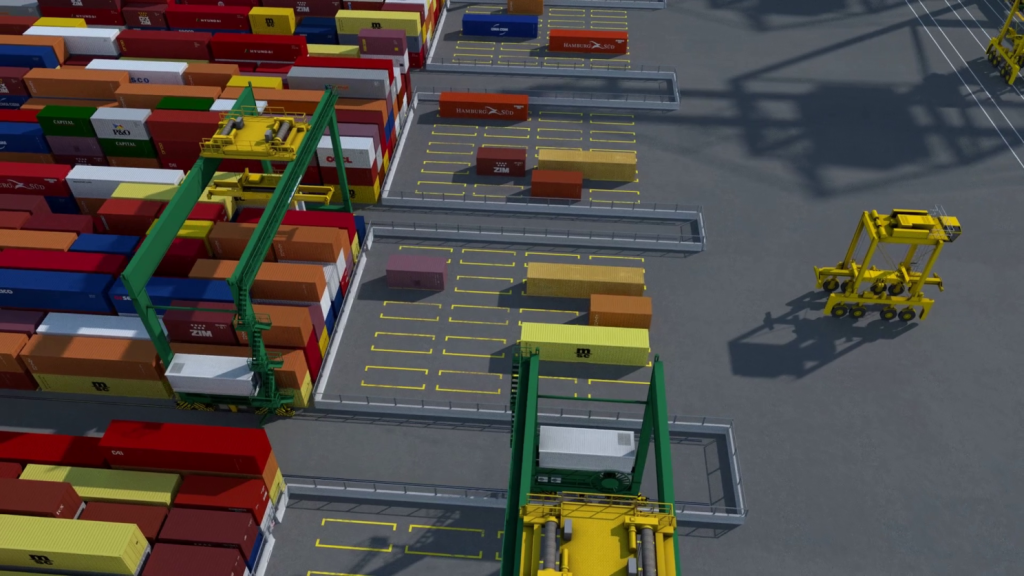
There is more (positive) impact of decoupling and that is that you can work ahead. You can already place containers in the buffer ahead of time, depending on how large the buffer is (in most ARMG terminals, the buffer is 16-20 TEU in size).
This is beneficial for two reasons:
1) It flattens peak load for the ARMG (if there are multiple QC’s drawing load containers from the same stack, it may become temporarily too much, so working ahead solves this).
2) If for a reason the next process has stopped (e.g. meal break, shift change), the ARMG can already work ahead, which will speed up the operations after the stop.
One of the questions that typically comes up is how large a buffer should be? This is typically a task #Portwise answers by using dynamic simulation models. These allow for accurate quantification of the effects of using different buffer sizes under realistic operational conditions (such as simultaneous loading and discharging operation). Generally, one can say that the bigger the buffer the better from an operational performance standpoint, as can be seen in the figure below. Besides, larger buffers come at the cost of e.g. reduced container storage space.
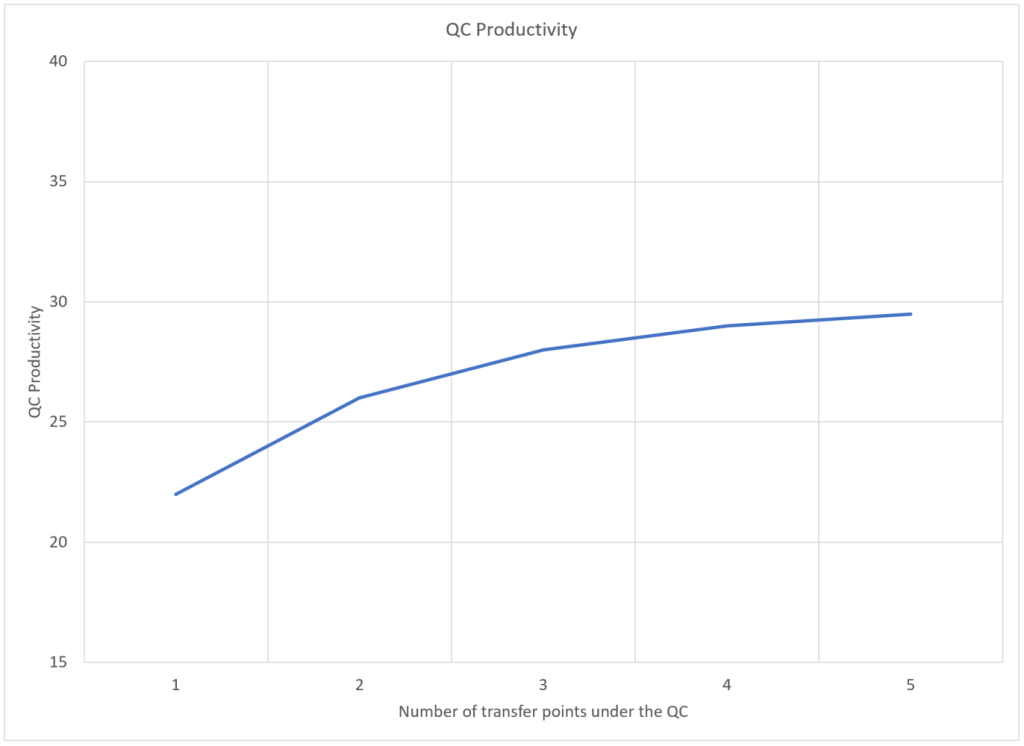
The most interesting buffer is the one under the QC. Here there is limited space, and it is needed for a multitude of tasks (OOG handling, a coning platform, a service lane) that conflict the enlargement of the buffer. #Portwise we tend to say that for non-tandem operations 3 buffer lanes suffice, and for tandem a fourth lane (2 pairs) are required.
Last (positive) remark I would like to make is about the TOS. Why is it easier to schedule and dispatch decoupled vehicles than coupled vehicles? The answer is simple: instead of having a great deal of interdependence, decoupled operations almost allow for independent scheduling; at least with quite some margin, if the “look ahead” is long enough (say 30 minutes plus). Then, the variations in the individual processes can be relieved by the buffer function inbetween the varying consecutive processes.
Is there nothing disadvantageous of decoupling then? I need to mention two downsides: first, upon a bay change, the shuttles or straddles need to wait until the QC has positioned itself, as the precise position of the QC needs to be determined before containers are dropped on the wrong ground position. Secondly, there is interference between shuttle carrier and QC, which sometimes slows down the QC, sometimes the Shuttle or Straddle Carrier.
However, the overall balance of decoupling capability is clearly positive: it’s an essential concept to make logistics flow.
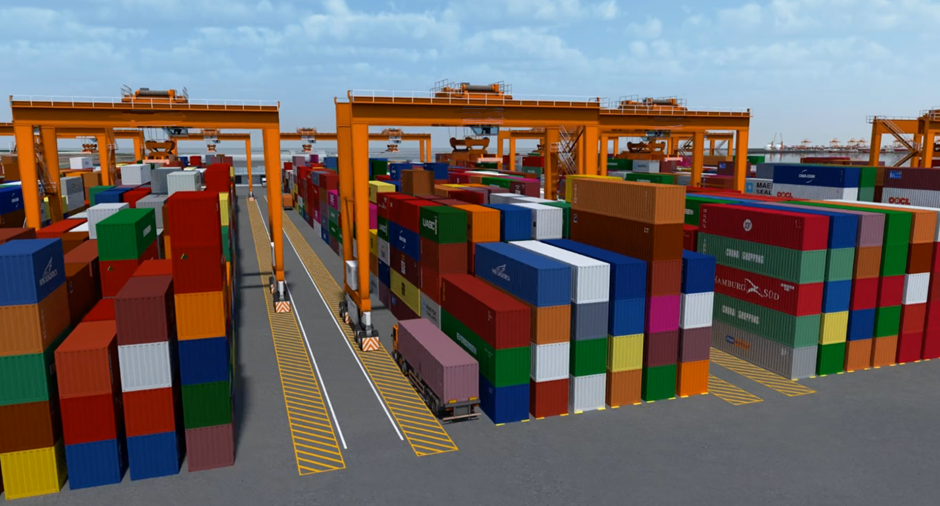
About the author: Yvo Saanen is a seasoned container terminal consultant who has worked for over 25 years in the industry, assisting terminal across the globe in getting the most out of their facility.